Optimizing Production Efficiency with Resin Granulators: A Key to Modern Manufacturing
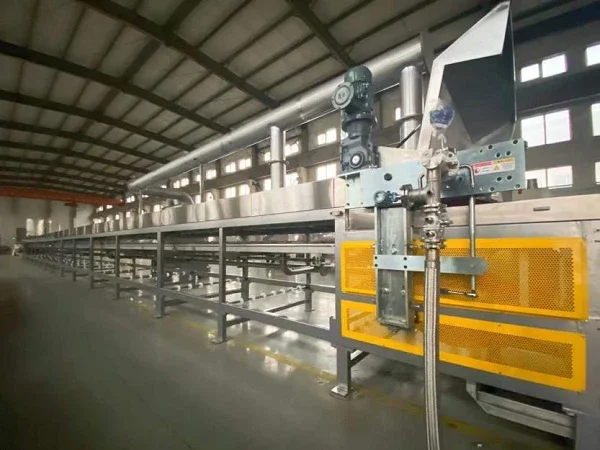
In modern manufacturing, the demand for precision, efficiency, and sustainability is ever-growing. As industries continue to optimize their production lines and minimize waste, the technology behind various processing equipment plays a pivotal role. Among the crucial machines used in diverse sectors, resin granulators stand out for their ability to precisely break down materials into uniform particles. This article Little Sky delves into the key features of resin granulators, as well as their contribution to improving manufacturing efficiency across industries.
What is a Resin Granulator?
A resin granulator is a specialized machine designed to break down larger pieces of resin into smaller granules or pellets. These granules are essential for subsequent processing, such as injection molding, extrusion, or compounding, which require uniform material size and consistency for optimal performance. Resin granulators operate through mechanical shearing or cutting, typically featuring rotating blades or knives that shred resin materials into uniform pieces. These machines are vital in industries that rely heavily on resin-based materials, such as plastics, chemicals, pharmaceuticals, and electronics. By creating smaller, manageable pieces of resin, the granulator ensures that manufacturers can process materials with greater precision and efficiency, improving both product quality and overall production speed.
Key Features of Resin Granulators
High Efficiency
Resin granulators are designed for maximum throughput. Their high cutting speeds allow them to handle large volumes of resin waste or raw material, ensuring continuous operation and reduced downtime. The granulation process minimizes material wastage by efficiently converting leftover resin into reusable particles. This not only supports sustainable practices by reducing waste but also ensures that manufacturers can produce high-quality materials for ongoing production.
Adjustable Particle Size
One of the most important aspects of resin granulators is their ability to produce resin particles of specific sizes. Depending on the application, manufacturers can adjust the granulator's settings to produce fine, medium, or coarse granules. This flexibility is essential for industries such as plastics, where material size directly affects the quality of the final product. By controlling the size of the resin granules, manufacturers can ensure a consistent and reliable flow of materials through downstream processing equipment such as injection molding and extrusion machines.
Durability and Reliability
Resin granulators are built to withstand the harsh conditions of industrial environments. They are made with high-quality materials and reinforced components to ensure long-lasting performance. The blades or knives in these machines are usually made from durable alloys, ensuring they can handle tough materials and operate efficiently for long periods. The robust construction reduces the frequency of maintenance and repairs, making resin granulators a reliable addition to any production line.
Energy Efficiency
Many modern resin granulators are designed to be energy-efficient, which helps companies reduce operational costs. By optimizing power usage, these machines contribute to greener manufacturing practices and can result in significant cost savings over time. With increasing pressure on industries to reduce their carbon footprint and energy consumption, energy-efficient resin granulators help companies meet environmental targets while still maintaining high productivity.
User-Friendly Control Systems
Resin granulators often feature advanced control systems that allow operators to easily adjust settings and monitor the granulation process. These systems are typically intuitive and provide real-time feedback on performance metrics, making it easier to identify issues and maintain optimal machine operation. Operators can adjust settings such as blade speed, granule size, and material feeding rate, ensuring that the granulator meets the specific needs of each production batch.
Resin granulators play a crucial role in modern manufacturing, offering benefits ranging from improved material efficiency to enhanced product quality. Their versatility in applications across industries such as plastic recycling, injection molding, extrusion, and pharmaceuticals makes them indispensable in the production of resin-based products. As industries continue to prioritize sustainability and efficiency, the demand for resin granulators will remain strong, further solidifying their place as an essential tool in manufacturing processes worldwide. By enabling the precise breakdown of resin materials into uniform granules, these machines support better production cycles, lower material waste, and higher-quality end products. As industries grow and evolve, resin granulators will continue to be at the forefront of optimizing manufacturing operations.
https://www.th-littlesky.com/Phenolic-Resin-Granulator-Supply.html
www.th-littlesky.com
Little Sky Mechanical Engineering Kabushiki Kaisha