The Top Reasons for Mechanical Seal Failure and How to Prevent Them
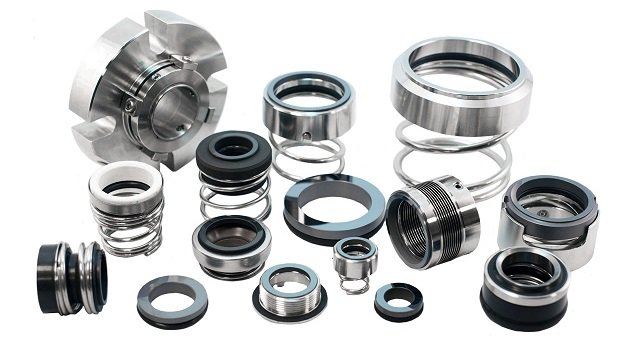
Mechanical seals are critical components in many industrial applications, including pumps, compressors, and mixers. They are designed to prevent leakage of fluids and gases and to maintain the integrity of the system. However, mechanical seal failure is a common problem that can lead to costly downtime, lost productivity, and even safety hazards. In this article, we will explore the top reasons for mechanical seal failure and provide practical tips on how to prevent them.
- Improper Installation
One of the most common causes of mechanical seal failure is improper installation. If the seal is not installed correctly, it can lead to misalignment, excessive vibration, and premature wear. To prevent this, it is essential to follow the manufacturer's installation instructions carefully and to ensure that the seal is installed by a qualified technician.
- Contamination
Contamination is another common cause of mechanical seal failure. If foreign particles, such as dirt, dust, or debris, enter the seal, they can cause damage to the sealing faces and lead to leakage. To prevent contamination, it is important to keep the system clean and to use appropriate filtration and straining devices.
- Overheating
Overheating is a significant cause of mechanical seal failure, particularly in high-temperature applications. If the seal is exposed to excessive heat, it can cause the sealing faces to warp or crack, leading to leakage. To prevent overheating, it is important to ensure that the system is properly cooled and that the seal is designed to withstand the operating temperature.
- Corrosion
Corrosion is another common cause of mechanical seal failure, particularly in applications where corrosive fluids are present. If the seal is exposed to corrosive substances, it can cause the sealing faces to pit or corrode, leading to leakage. To prevent corrosion, it is important to select a seal material that is resistant to the corrosive fluid and to ensure that the system is properly maintained.
- Wear and Tear
Finally, wear and tear are inevitable causes of mechanical seal failure. Over time, the sealing faces will wear down, leading to leakage. To prevent wear and tear, it is important to select a seal material that is appropriate for the application and to ensure that the system is properly maintained and lubricated.
In conclusion, mechanical seal failure can be a costly and disruptive problem in industrial applications. However, by understanding the top causes of failure and taking appropriate preventive measures, it is possible to minimize the risk of failure and ensure the long-term reliability of the system. By following the tips outlined in this article, you can help to prevent mechanical seal failure and keep your system running smoothly.