Unlocking the Power of Bolted Joints: Applications and Advancements
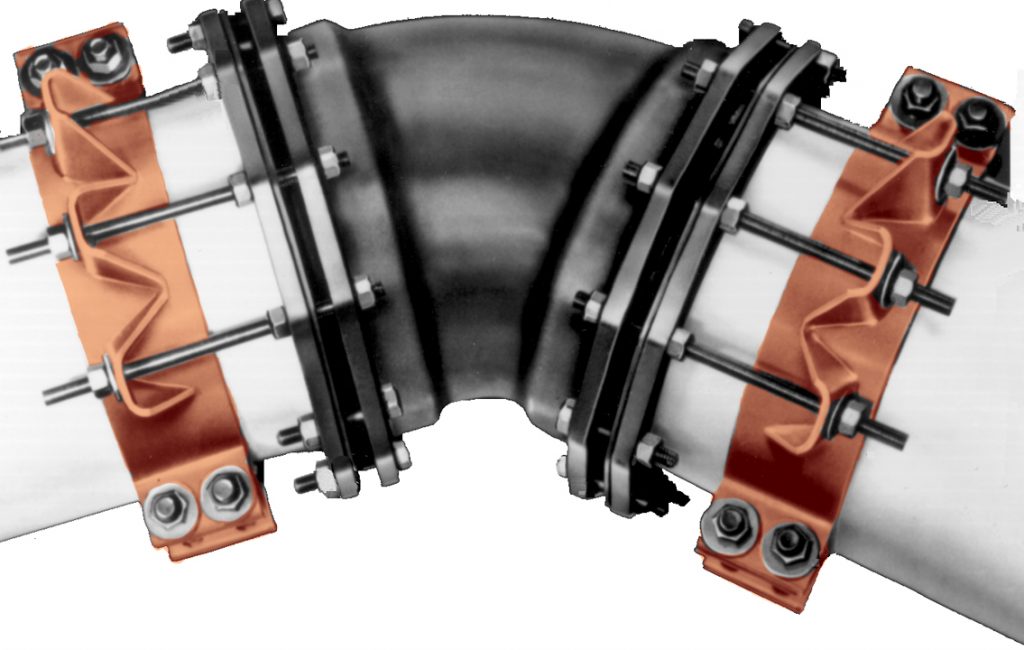
Bolted joints play a crucial role in various industries, providing secure and reliable connections between components. From construction and automotive to aerospace and manufacturing, bolted joints are widely used for their strength, versatility, and ease of assembly. In this blog post, we will delve into the world of bolted joints, exploring their applications, advancements, and the key factors to consider for optimal performance.
- Understanding Bolted Joints:
A bolted joint is a mechanical connection formed by tightening a bolt or multiple bolts to clamp two or more components together. It relies on the principle of friction and preload to maintain the integrity of the joint. Unlike other fastening methods, such as welding or adhesives, bolted joints offer the advantage of disassembly and reusability, making them ideal for applications that require maintenance, repairs, or modifications. - Applications of Bolted Joints:
2.1 Structural Engineering:
In structural engineering, bolted joints are extensively used to connect steel beams, columns, and other structural elements. These joints provide the necessary strength and rigidity to withstand heavy loads, seismic forces, and dynamic vibrations. The ability to easily disassemble and replace bolts makes bolted connections highly desirable in construction projects.
2.2 Automotive Industry:
Bolted joints are vital in the automotive industry, where they secure critical components such as engine parts, suspension systems, and body panels. The high-strength bolts used in these applications ensure the structural integrity of vehicles, enhance safety, and facilitate efficient assembly processes on the production line.
2.3 Aerospace and Defense:
In the aerospace and defense sectors, bolted joints are employed in aircraft assembly, missile systems, and spacecraft. These applications demand lightweight yet robust connections that can withstand extreme conditions, including high temperatures, vibrations, and aerodynamic forces. Advanced materials, such as titanium alloys and composites, are often used to optimize the strength-to-weight ratio of bolted joints in these industries.
2.4 Machinery and Manufacturing:
Bolted joints find extensive use in machinery and manufacturing equipment, where they provide secure connections for rotating parts, gearboxes, and assembly lines. The ability to easily adjust and align components during installation or maintenance is a significant advantage of bolted joints in these applications. Additionally, advancements in bolted joint design, such as self-locking nuts and torque control systems, have improved reliability and operational efficiency.
- Advancements in Bolted Joint Technology:
3.1 Preload and Tightening Techniques:
Achieving the correct preload, or the initial tension in a bolted joint, is critical for its performance. Advancements in preload measurement techniques, such as ultrasonic and strain gauge methods, have enabled more accurate and reliable tightening processes. Additionally, the development of torque control tools and tensioning devices has improved the consistency and uniformity of bolted joint assembly.
3.2 Coatings and Surface Treatments:
To enhance the performance and longevity of bolted joints, various coatings and surface treatments are employed. These include corrosion-resistant coatings, such as zinc plating and epoxy coatings, as well as lubricants and thread-locking compounds. These treatments protect against environmental factors, reduce friction, and prevent loosening or galling of the joint.
3.3 Computational Modeling and Simulation:
Advancements in computational modeling and simulation techniques have revolutionized the design and analysis of bolted joints. Finite element analysis (FEA) and virtual testing allow engineers to predict the behavior of joints under different loading conditions, optimize designs, and identify potential failure points. This enables more efficient and cost-effective development processes, reducing the need for physical prototypes and extensive testing.
Conclusion:
Bolted joints are indispensable in numerous industries, providing secure and versatile connections that withstand demanding conditions. From structural engineering to automotive, aerospace, and manufacturing, the applications of bolted joints are vast and diverse. With advancements in technology, materials, and design methodologies, bolted joints continue to evolve, offering improved performance, reliability, and efficiency. By understanding the principles and advancements in bolted joint technology, engineers and manufacturers can unlock the full potential of these connections, ensuring safe and robust assemblies in their respective fields.