Relay vs. Transistor Output PLC: Unveiling the Distinctions and Applications
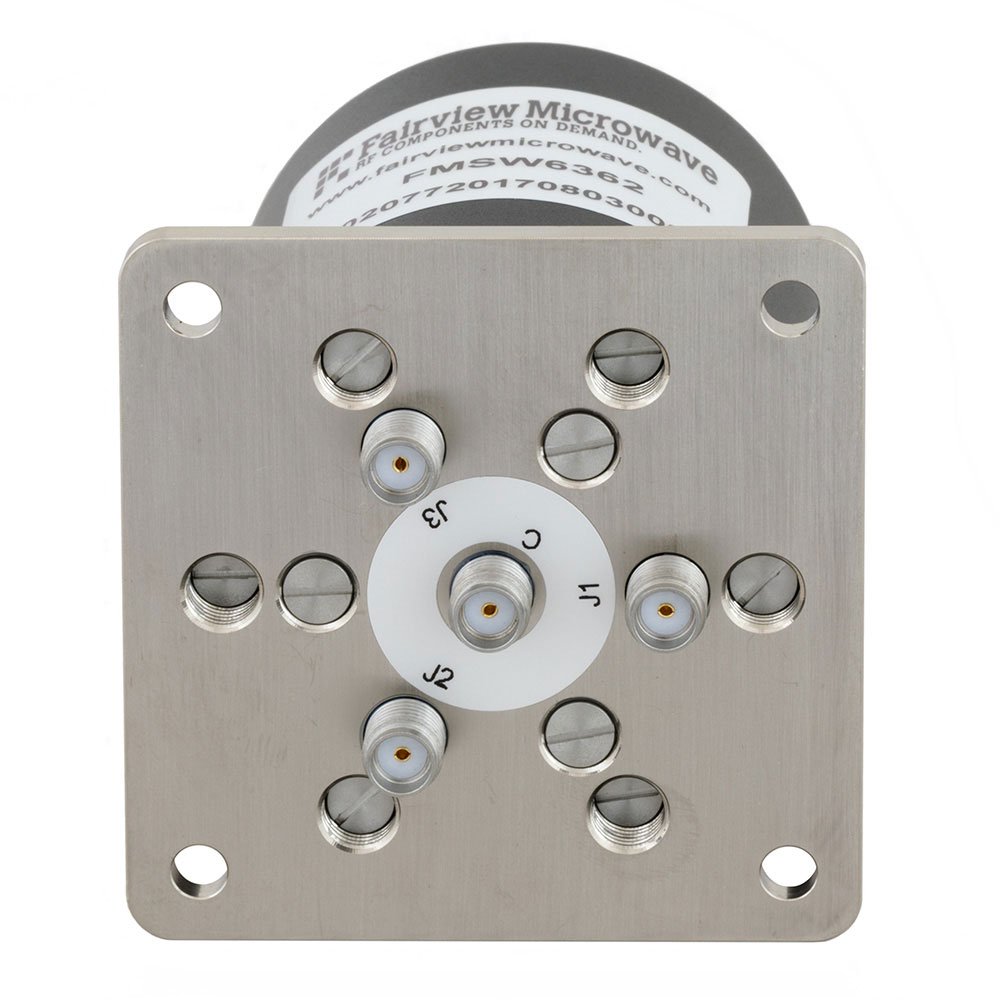
In the realm of industrial automation, Programmable Logic Controllers (PLCs) play a pivotal role in controlling and monitoring various processes. PLCs are available in different types, each with its own unique features and applications. In this article, we will delve into the differences between two commonly used PLC output types: relay output and transistor output. Understanding these distinctions is crucial for selecting the appropriate PLC for specific industrial requirements.
- Functionality:
Relay Output PLC:
Relay output PLCs utilize electromechanical relays to switch electrical loads. These relays consist of a coil and a set of contacts that open or close based on the control signal received from the PLC. This output type is suitable for applications requiring high current or voltage switching capabilities.
Transistor Output PLC:
Transistor output PLCs, on the other hand, employ solid-state transistors to control electrical loads. These transistors act as electronic switches, allowing or blocking the flow of current based on the control signal. Transistor output PLCs are ideal for applications that demand fast switching speeds and lower power consumption.
- Advantages and Disadvantages:
Relay Output PLC:
- Advantages:
- Can handle high current and voltage levels.
- Offers galvanic isolation, protecting the PLC from external disturbances.
- Suitable for both AC and DC loads.
- Disadvantages:
- Slower switching speeds compared to transistor output PLCs.
- Limited lifespan due to mechanical wear and tear.
- Bulkier in size and require more space in control panels.
Transistor Output PLC:
- Advantages:
- Faster switching speeds, enabling precise control of processes.
- Longer lifespan due to absence of mechanical components.
- Compact in size, allowing for space-efficient installations.
- Disadvantages:
- Limited current and voltage handling capabilities.
- Susceptible to damage from voltage spikes or electrical noise.
- Not suitable for high-power applications.
- Applications:
Relay Output PLC:
Relay output PLCs find extensive use in industries such as manufacturing, power distribution, and heavy machinery control. They are well-suited for applications involving motor control, solenoid valve operation, and high-power switching.
Transistor Output PLC:
Transistor output PLCs are commonly employed in industries requiring precise control and rapid response times. They are ideal for applications like robotics, semiconductor manufacturing, and automated assembly lines. Additionally, their low power consumption makes them suitable for battery-powered systems.
Conclusion:
In summary, the choice between a relay output PLC and a transistor output PLC depends on the specific requirements of the industrial application. Relay output PLCs excel in high-power scenarios, while transistor output PLCs offer faster switching speeds and compact designs. By understanding the distinctions and applications of these PLC output types, engineers and automation professionals can make informed decisions to optimize their processes.