The Inner Workings of PLC Relays: Unveiling the Power Behind Industrial Automation
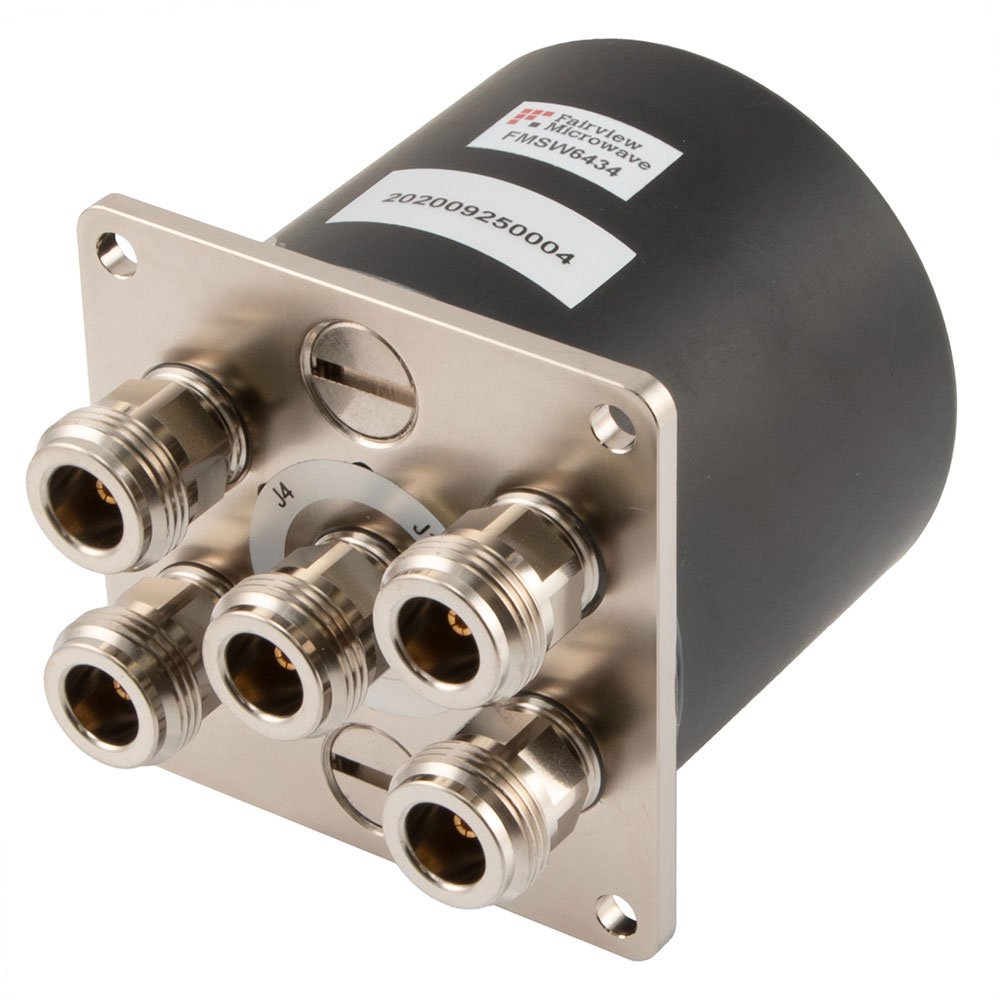
In the realm of industrial automation, Programmable Logic Controllers (PLCs) play a pivotal role in controlling and monitoring various processes. At the heart of a PLC lies the relay, a fundamental component that enables the seamless execution of complex tasks. In this article, we will delve into the inner workings of relays in PLCs, exploring their functionality, types, and applications.
- Understanding the Basics of Relays:
Relays serve as electrically operated switches, allowing the control of high-power circuits with low-power signals. In a PLC, relays act as the interface between the input and output modules, facilitating communication between the controller and the external devices. They are designed to handle different voltage and current levels, ensuring the safe and efficient operation of industrial machinery. - How Relays Work in PLCs:
When an input signal is received by the PLC, it triggers the corresponding relay, which then switches the output circuit on or off. This process involves several key steps:
a. Input Signal Detection: The PLC continuously monitors the input modules for any changes in the signal status. Once a change is detected, the PLC sends a command to the appropriate relay.
b. Relay Activation: Upon receiving the command, the relay's coil is energized, creating a magnetic field. This field attracts the relay's armature, causing it to move and establish a connection between the input and output circuits.
c. Output Circuit Control: With the relay's contacts closed, the output circuit is either energized or de-energized, depending on the desired operation. This allows the PLC to control motors, solenoids, valves, and other industrial devices.
- Types of Relays Used in PLCs:
PLC relays come in various forms, each tailored to specific applications. Some common types include:
a. Electromechanical Relays: These relays use an electromagnetic coil to control the switching mechanism. They are versatile and widely used in PLCs due to their reliability and ability to handle high currents.
b. Solid-State Relays (SSRs): SSRs employ semiconductor devices, such as thyristors or triacs, to perform switching operations. They offer faster response times, longer lifespan, and enhanced noise immunity compared to electromechanical relays.
c. Reed Relays: Reed relays utilize a hermetically sealed glass tube containing two metal reeds. When a magnetic field is applied, the reeds attract each other, completing the circuit. They are commonly used in applications requiring high switching speeds and low power consumption.
- Applications of Relay in PLCs:
Relays in PLCs find extensive use in various industrial sectors, including:
a. Manufacturing: PLC relays control conveyor belts, robotic arms, and assembly lines, ensuring precise and synchronized operations.
b. Energy Management: They regulate power distribution, monitor energy consumption, and control lighting systems, optimizing energy efficiency.
c. Building Automation: Relays enable the control of HVAC systems, access control, and fire alarm systems, enhancing safety and comfort in commercial buildings.
d. Process Control: PLC relays play a crucial role in managing complex processes, such as water treatment, chemical production, and food processing, ensuring accuracy and reliability.
Conclusion:
Relays are the unsung heroes of PLCs, enabling seamless communication between the controller and external devices. Understanding their inner workings and applications is essential for engineers and technicians involved in industrial automation. By harnessing the power of relays, PLCs revolutionize the way industries operate, paving the way for increased efficiency, safety, and productivity.